A NOVEL INDUSTRIAL MODEL OF PLANT FACTORY BASED ON CLOUD SERVICE
Proceedings of the 8th International Symposium on Machinery and Mechatronics for Agriculture and Biosystems Engineering (ISMAB)
23-25 May 2016, Niigata, Japan
​
Ming-Yen Lin, Szu-Yu Lin, Chao-Lin Yang, Yu-Hsiang Lin, Min-Hsiung Hung, Jui Jen Chou
Abstract
Abstract: In this study we developed a cloud service system to serve as a community for plant factory equipment providers, crop growers and cultivation/engineering experts. With the system, the services in the field of plant factory can be shared and used effectively among these collaborators or business partners. The services consist of turnkey technology for plant factory construction, optimal control strategy for crop growth, system control/monitoring and decision making for business management. Moreover, the developed system can improve the protection of intellectual property of the technical knowhow. Our system includes four parts: the cloud service platform, the service providers, the service demanders and control/monitoring systems. The cloud service platform acts as service brokers to match or integrate services providers and demanders in the plant factory industry together. For example, if a crop grower who wants to start up crop mass production with a plant factory, the facilities or knowhow necessary to run it with certain specifications can be established and acquired through our system. In addition, our system can also record any activities or behaviors of service demanders and providers, which are extracted to provide better prediction greater operational efficiency, higher quality decision making, cost reduction and risk minimization.
Key Words: Plant Factory, Cloud Service, Control, Monitor, Crop Production. Big Data
Introduction
Food demand dramatically increases with the growth of worldwide population. However, due to extreme climate conditions caused by global warming, it is certain that traditional agriculture techniques will face more challenges. Such a highly controlled and recycling artificial environment like plant factory could not only optimize the consumption of water but also guarantee steady harvest of crops with consistent quality without being subjected to natural weather’s fluctuation. Furthermore, it could prevent crops from harmful chemical contaminations like fertilizer, pesticide or atmospheric particulate produced by fossil fuel in natural farming, therefore producing untainted and safe crops for customers.
IoT-related techniques have been successfully applied to the plant factory industry (Chen et al. 2013, Harun et al., 2014; Israni et al., 2015; Park and Yoe., 2015; Yuan et al. 2015). Intellectualized cultivation environment regulation and monitoring is currently achieved and the following work would be aimed at the development of cloud service platform (Shimizu et al., 2015; TongKe, 2015).
The plant factory industry can be roughly divided into the service providers and demanders. The former corresponds to experts and equipment industries, while the latter implies the personnel that manage or operate the plant factory directly. The goal of our research is to develop a cloud service platform serving as a commutative gateway between those two. In addition, this platform also integrates the management and monitoring tasks of the plant factory. Eventually, a new business model of the industry would be developed.
Materials and Methods
Our research develop an integrated cloud service system composed of the cloud service platform, the service providers, the service demanders and the control/monitoring systems in order to solve the aforementioned problem. The system architecture is shown in Fig. 1.

Fig.1 The structure of the cloud service system.
Control / Monitoring System
The control/monitoring systems are mounted on local plant factory equipment. The role of it is to serve as a controller and collector to manipulate lights, fans or electrical switches and record the environmental parameters like humidity, temperature, brightness or anything crucial for crops growth. Any action of the local system is based on the commands from cloud side.
The monitoring system utilizes Raspberry Pi and Arduino as the upper and lower controllers respectively, featuring low cost and high flexibility. For instance, the system can easily be applied to different types of plant factories varying from small, experimental ones to large, mass productive ones.
We place a web service on Raspberry Pi serving as a manager receiving requests from the cloud site and therefore, giving control commands to its employee’s - Arduino. It collects and stores sensor data unwrapped by Arduino and also records, converts and streams audio and video data form webcams to the cloud site. As for Arduino, the job is to control digital inputs/outputs on each electrical switch and moreover; it converts those low-level binary data such as RS232, I2C or SPI communication protocols from sensors into high-level data form like integer or string and send them to its supervisor - Raspberry Pi. In sum, such the work assignment and collaboration can assure the best performance of the whole system.
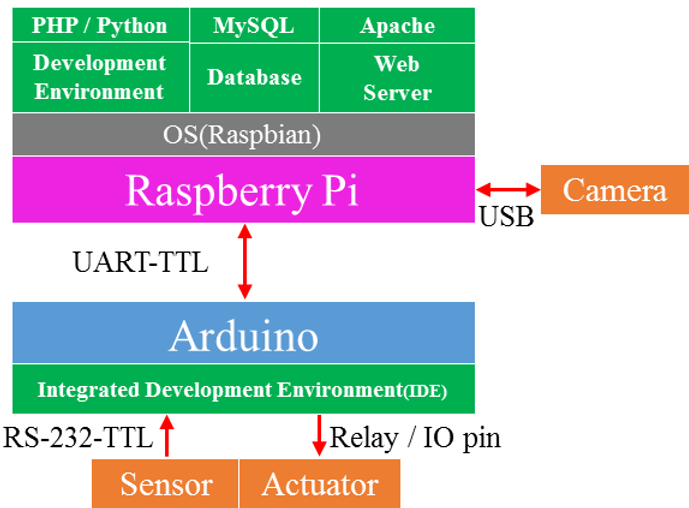
Fig. 2 Structure of control and monitoring system
Service Demanders
The service demanders refer to those who actually engage in managing or utilizing plant factory to fulfill their needs. The needs are to increase the efficiency and flexibility of supply chains in food production, the optimized approach to maintenance their facilities in limited budget, the intellectual properties’ protection during any business collaboration and just to name a few. The using of plant factory in different application is an interdisciplinary work. For demanders who want to engage in massive crops production, the primary goal is to make the best profit and to ensure the stability of their supply chain. Therefore, they may require experts in agriculture and the ones in business management. For researchers who want to find the air-conditioner’s influence in sprout’s growth, they may need engineers in mechatronics and people skilled in Botany.
Service Providers
Experts of crop cultivating, operation and suppliers of facilities required in the plant factory industrial, are known as the service providers.
Cloud Service Platform
The cloud service platform is an integrating system based on cloud communication. Various kinds of services are established thereon for demanded purposes, such as the providing of professional intellectual property management, bonus and security mechanisms. Furtherly, management or promoting tasks of interspersed plant factories is assisted by utilizing remote control techniques, moreover, expert knowledge and supplier technology of different professional fields could be integrated to provide customized service.
The cloud service platform provides a service application interface through Web Services Description Language (WSDL), adopting Simple Object Access Protocol (SOAP) as the communication protocol for data transmission in order to communicate with the gateways, eventually integrating the control/monitoring system and the cloud service platform to provide demand-related applications. Various types of service functions, for instance, extraction of environmental parameters, user attempt record or expert intermedium service, could be developed on the cloud service platform.
The browser/server architecture is adopted in the system development so as to enable convenient operation and platform crossover for different users.

Fig. 3 The interface of web service.
Results and Discussion
In regard to the system’s overall operating process, the documented knowledge from plant factory experts are well arranged and stored in cloud database which is available for those who have permission to access. Users can become official service demanders through simple online application and access the plant factory related data or information depending on their payment. Although they have full permission to extract the operating information from cloud database such as environmental parameters for crops which could be used to refine their systems directly, however, access to detailed information would be limited. The working pattern or any parameters about how to refine their production will be directly downloaded to local servers and executed by those machines. Accordingly, the experts’ intellectual property could be protected. In addition, the demander’s environmental parameters could be uploaded to the system during the whole process mentioned above to customize the control pattern.
The approach to Integrate plant factory experts and equipment suppliers into the cloud service platform allows us to avoid repeated and redundant research. The integration can solve the problem of compatibilities among different system interfaces from different equipment suppliers. Our system can also cut down the equipment suppliers’ fee in advertisement and promotion. Moreover, by combining the expert knowledge and patented technology from equipment suppliers, the equipment suppliers could therefore modify and enhance the applicability of their products.
Cost reduction of product commercialization is commonly progressed via process standardization and mass production. On the other hand, our system adopts expert suggestion and knowledge to customize products and enhance additional values.
Based on what we mentioned above, such the concepts of cloud technique fusing agricultural professions and plant factory equipment management services achieves consolidating various industries from service demanders, experts and equipment suppliers, it can reduce cost, provide intellectual property security and increase profits.
In practical operation, application for authority access of the cloud service platform should be included before constructing and operating a plant factory system.
Proposed request for constructing a plant factory would be sent to industries providing related services, who also applied to join the cloud system.
The industry provides various selective service programs orient to the demander’s requests and would subsequently run the construction process based on the optimized selection.
Operation related requests could be proposed after completion of the plant factory construction, all kinds of programs and selections would be provided, similarly.
Operating request proposals and solutions via cloud platform could minimize time spent on comparison and selection, while valuation tasks could be guaranteed fair and impartial due to operating through the cloud platform as well.
Solutions could be found on the cloud platform when the plant factory operation encounters problems.
During the plant factory operation process, related operation data could be stored in the cloud dataset via cloud system. Besides tracking the origins of any problems occurred, the data could also benefit in the improvement of expert information.
Moreover, mass cultivation was required formerly to obtain these planting data, yet these could be widely provided nowadays through industries who joined the system, researchers in related areas could also run analyses and examinations attributed to access for the data.
Take the red lines in Fig. 1 as an example.
E.0: A user on client side downloads GUI and logins the system.
E.1: The user creates an order of expert and/or equipment broker requirements by GUI.
E.2: The GUI calls the expert and equipment broker service on the cloud.
E.3: The cloud service sends the order to the gateway on professional service side, which will save the order into the local database and notify the service person of the received order.
E.4: The service person operates the service system to retrieve the information of recommended professional service labs and equipment suppliers, which fit the order requirements, from database.
E.5: The service person contacts with the desired expert and equipment supplier to create the advisory data corresponding to the order.
E.6: The service person sends the advisory data to the user on client side by the expert and equipment broker service on the cloud.
So the experts and equipment suppliers could be brokered to the demander by the cloud system.
Conclusions
Apart from providing assistance to the plant factory management and monitoring tasks, the cloud service system architecture our research develop could also integrate service providers and demanders in the plant factory industry, eventually forming a business model. Moreover, expert knowledge could effectively promote the plant factory operation under intellectual property security.
Further work involving service function update and modularization based on cloud system program optimization is expected to integrate more service providers and demanders of various types into our system.
References
Chen, J. I. Z., Y. C. Chen, and S. D. Chung. 2013. Implementation of a greenhouse crop remote monitoring system with IOT technology. In Taiwan Academic Network Conference. 657-661.
Harun, A. N., R. Ahmad, and N. Mohamed. 2014. Far red flowering control treatment for Brassica chinensis in indoor farming utilizing wireless sensor network. In Proceedings of the 14th Internationa l Conference on Robotics, Control and Manufacturing Technology (ROCOM '14) .147-155.
Israni, S., H. Meharkure, and P. Yelore. 2015. Application of IOT based system for advance agriculture in India. International Journal of Innovative Research in Computer and Communication Engineering. 3(11): 10831-10837.
Park, J. and H. Yoe. 2015. Greenhouse environment monitoring and control system using CoAP. Advanced Science and Technology Letters Vol.95, 168-172.
Shimizu, S., N. Sugihara, N. Wakizaka, K. Oe and M. Katsuta. 2015. Cloud services supporting plant factory production for the next generation of agricultural businesses. Hitachi Review. 64(1): 63-68.
TongKe, F. 2015. Smart Agriculture Based on Cloud Computing and IOT. Journal of Convergence Information Technology(JCIT) 8(2): 210-216.
Yuan, M., T. Shieh, G. Lu and Y. Lin. 2014. The Applications of Industrial Engineering in Agriculture Production Management. In 5th International Asia Conference on Industrial Engineering and Management Innovation (IEMI 2014). 403-408.